Key Takeaways
Don’t have time to read the full guide? No problem. Here are the most critical diagnostic techniques you can use to pinpoint marine engine problems faster and more accurately. These scannable insights blend foundational principles with modern data-driven methods to make your next repair more efficient.
- Start with your senses before touching any tools. A thorough visual, auditory, and olfactory inspection is your most cost-effective first step, often revealing leaks, worn parts, or corrosion that electronic scanners can’t see.
- Leverage the ECM’s full story, not just its fault codes. Analyze the engine run history to understand how the vessel was operated and review live data parameters to validate dashboard gauge accuracy in real time.
- Validate codes with mechanical tests to find the root cause. A fault code tells you what happened, but a compression or leak-down test tells you why by directly assessing the engine’s internal mechanical health.
- Prioritize cooling system checks to prevent catastrophic failure. Overheating is a destructive and common issue, so regularly inspect the raw water impeller and use an infrared temp gun to find hot spots on manifolds before they cause damage.
- Isolate fuel and air delivery issues with targeted tests. For performance problems, always conduct fuel pressure and volume tests and use diagnostic software to perform an injector cut-out test to pinpoint the faulty component.
- Replicate problems with a sea trial for intermittent issues. Some faults only appear under a true, real-world load on the water, which is impossible to simulate accurately on a trailer with a flush hose.
- Capture elusive failures by logging live data during sea trials. Using diagnostic software to graph and record engine parameters turns a fleeting, hard-to-diagnose glitch into concrete, solvable evidence.
Master these techniques by diving into our complete guide for in-depth explanations and pro tips on each diagnostic step.
Introduction
The engine runs like a top on the flush muffs. But once it’s in the water and under load, it bogs down, throws an alarm, or just doesn’t feel right. It’s a classic scenario that sends even seasoned technicians chasing intermittent ghosts.
With today’s complex marine engines, simply pulling a fault code is rarely the final answer. More often, it’s just the first clue in a much deeper investigation.
Effective diagnosis isn’t about having a lucky guess. It’s about executing a systematic, repeatable process that blends old-school fundamentals with modern data analysis. This approach is the key to faster solutions, fewer comebacks, and more confident repairs.
We’ll walk you through a complete workflow that shows you how to:
- Uncover critical clues with a thorough sensory inspection
- Go beyond fault codes to interpret the engine’s full data story
- Use targeted mechanical tests to pinpoint the root cause
- Leverage sea trials to solve the most elusive on-water problems
Mastering this method transforms you from a parts-changer into a true diagnostician. It all begins by trusting the most powerful and readily available tools you have—long before you ever plug in a scanner.
The Foundational Diagnostic Approach: Start with Your Senses
Before you ever plug in a diagnostic scanner, a thorough sensory inspection provides critical clues that guide your entire process.
This initial assessment is non-invasive, costs nothing, and often pinpoints the problem area immediately. Think of it as building a case file on the engine’s condition, saving you valuable time and effort down the line.
Performing a Systematic Visual Inspection
A methodical visual check is the bedrock of any marine engine diagnosis. It’s about training your eye to spot the physical abnormalities and wear patterns that electronic tools simply cannot see.
- Look for Leaks: Carefully inspect all fluid systems. Check for engine oil, coolant, fuel, and hydraulic fluid. Look for tell-tale stains on the engine block, in the bilge, and around all hoses and fittings.
- Examine Hoses and Belts: Check for cracked, bulging, or soft hoses by giving them a light squeeze. Inspect serpentine and v-belts for glazing, fraying, or excessive slack that could signal an impending failure.
- Assess Wiring and Connections: Look for corroded terminals, chafed wires, and loose connections. Pay close attention to the battery, starter, and sensor plugs, as these are common trouble spots.
- Check for Corrosion: Saltwater environments are brutal. Inspect the engine block, exhaust manifolds, risers, and cooling system for signs of internal or external corrosion that could restrict flow or cause leaks.
The Importance of Auditory and Olfactory Clues
Your ears and nose are powerful diagnostic tools that can detect serious issues before they become catastrophic failures.
Listen to the engine at startup, idle, and if possible, under load.
- Unusual Sounds: A sharp knock could mean bearing issues, a persistent tick can point to valve train problems, and a grinding noise often relates to the starter or gear systems.
- Abnormal Smells: A strong fuel smell indicates a leak. The scent of burning oil or rubber points to leaks or failing belts, while a distinctively sweet smell is the classic sign of a coolant leak.
This sensory-first approach doesn’t just find obvious problems; it creates a complete picture of the engine’s health, making every subsequent electronic or mechanical test more targeted and effective.
Harnessing Electronic Diagnostics: Interfacing with the Engine Control Module (ECM)
Modern marine engines rely on a sophisticated Engine Control Module (ECM) that acts as the engine’s brain. Tapping into this system is the fastest way to get a high-level overview of its health and history.
This step transforms diagnostics from guesswork into a data-driven science, providing a clear path forward before you even pick up a wrench.
Connecting to the ECM: Tools of the Trade
Accessing the ECM requires specialized hardware and software. Investing in the right tools pays for itself through dramatically increased accuracy and efficiency.
You will need two key components:
- Diagnostic Adapters: The correct physical cable and adapter are required to connect your computer or scanner to the engine’s diagnostic port.
- Scanning Software: Your choice here depends on the depth of information you need.
- PC-Based Systems like Jaltest Marine or Diacom Marine offer comprehensive, dealer-level functionality. They provide live data graphing, component tests, and detailed reporting.
- Handheld Scanners are more portable for quick code reading and clearing but offer less in-depth analysis.
Interpreting Data: Beyond Just Fault Codes
The ECM provides a wealth of information that goes far beyond a simple “check engine” light. Knowing what to look for is the key to an accurate diagnosis.
- Active vs. Stored Fault Codes: This is your starting point. Active codes point to a current, ongoing problem, while stored codes reveal intermittent issues or past faults.
- Engine Run History: This data is a goldmine. You can see not just total engine hours, but a full breakdown of time spent at different RPM ranges. This tells you how the boat has been operated—a story the hour meter alone can’t tell.
- Live Data (Parameters): Watch real-time sensor readings for oil pressure, coolant temp, and RPM. This is the best way to validate dashboard gauge accuracy and confirm sensors are functioning correctly.
Connecting to the ECM isn’t just about pulling codes; it’s about building a complete data profile of the engine. This allows you to see its past operational history and its current performance in real-time, providing the critical context needed for an effective and efficient repair.
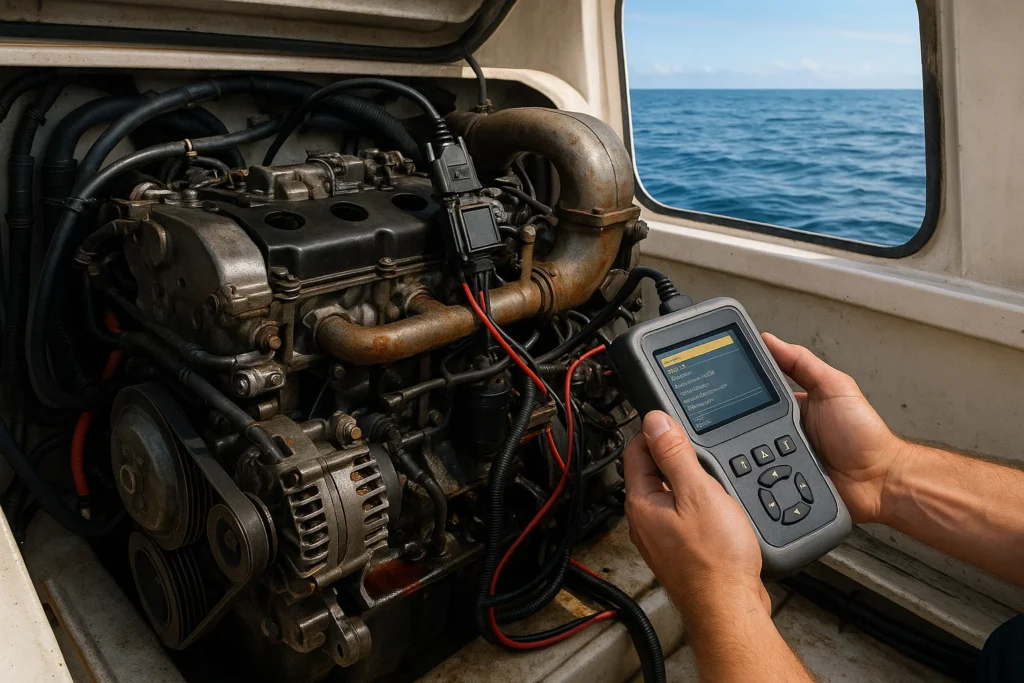
Beyond the Codes: Essential Mechanical and System-Specific Testing
Fault codes point you in the right direction, but they rarely tell the whole story.
A code for “misfire cylinder 3” tells you what happened, but not why. That’s where targeted mechanical tests come in to validate the electronic data and find the true root cause of the failure.
Assessing Internal Engine Health
These tests go straight to the heart of the engine, evaluating the core mechanical integrity of its combustion chambers.
- Compression Testing: This foundational test measures the pressure each cylinder can build. A single low cylinder often points directly to a bad valve, worn piston rings, or a head gasket issue.
- Cylinder Leak-Down Testing: This is a more precise diagnostic. By pumping compressed air into a cylinder, you can listen for where it escapes—from the exhaust, the intake, or into the crankcase—pinpointing the exact location of a seal failure.
Verifying Fuel and Air Delivery
Proper fuel and air delivery is non-negotiable for engine performance. Fault codes related to fuel trim or oxygen sensors almost always lead you here.
- Fuel Pressure and Volume Tests: A simple gauge check confirms the pump is delivering fuel at the right pressure, while a volume test ensures it can supply enough fuel when the engine is under a heavy load.
- Injector Cut-Out Test: Using professional software like Jaltest, you can electronically disable one injector at a time. The cylinder that doesn’t cause a drop in RPMs instantly reveals the faulty injector.
Tackling Critical Cooling System Failures
Overheating is one of the most common and destructive issues a marine engine can face. These checks are essential for both prevention and diagnosis.
- Impeller and Water Pump Inspection: The raw water pump impeller is a notorious failure point. It should be inspected regularly and replaced as part of routine maintenance.
- Thermostat Testing: A stuck thermostat (either open or closed) will prevent the engine from maintaining its proper operating temperature, causing it to run too hot or too cold.
- Manifold and Riser Inspection: Use an infrared temperature gun to find dangerous hot spots on exhaust manifolds and risers. This indicates internal blockages from rust and scale that restrict water flow.
Remember, digital fault codes are just the first clue. True diagnostic mastery comes from using that information to guide hands-on mechanical testing, which provides the definitive answers needed for an effective and lasting repair.
Dynamic Diagnosis: The Power of Live Data and Sea Trials
Some engine problems are ghosts. They only appear under specific conditions—like at high RPM, under heavy load, or after the engine fully warms up.
A static test in the workshop will never find these issues. This is where dynamic testing, including sea trials with live data logging, becomes your most powerful tool for solving complex, intermittent problems.
Why a Sea Trial is Non-Negotiable
A sea trial isn’t just a boat ride; it’s a controlled experiment designed to replicate the exact conditions where a problem occurs.
The goal is to move beyond theory and see the issue firsthand.
- Validate the Complaint: First, confirm the customer’s report. Does the engine truly hesitate at 3,000 RPM? Does an alarm only sound after 20 minutes of cruising?
- Test Under Real Load: Running the engine in the water puts a true, real-world load on it that simply can’t be simulated on a trailer with a flush hose. This is critical for diagnosing issues with fuel delivery, turbo performance, and overheating.
From Live Data to Definitive Answers
While on the water, connecting a high-level diagnostic tool like Jaltest Marine or TEXA Diagnostics lets you see a complete picture of the engine’s performance in real time.
You can monitor dozens of key parameters simultaneously. For an overheating issue, you’d watch coolant temperature, raw water pressure, and engine load all on one screen. For a performance lag, you’d track RPM, fuel trim, and boost pressure.
Capturing the Moment of Failure
Modern software can graph these data streams, making it easy to spot correlations. Imagine seeing fuel pressure drop sharply on the graph at the exact instant the RPMs begin to sag.
The data logging feature is even more powerful. You can record the entire trial, trigger the problem, and then review the data frame-by-frame back at the shop.
This process turns a fleeting, intermittent glitch into concrete, solvable data.
Dynamic testing with live data logging is the final word in diagnostics. It allows you to stop guessing and start seeing, providing the hard evidence needed to fix the most elusive engine problems with confidence.
Conclusion
Moving from a good technician to a great diagnostician isn’t about memorizing every fault code. It’s about adopting a systematic, multi-layered approach that turns complex problems into clear, solvable puzzles.
By blending old-school sensory inspection with modern data analysis, you stop guessing and start proving. This method builds confidence, reduces comebacks, and saves immense time and money.
Your Diagnostic Blueprint
Here are the core principles to integrate into every engine repair:
- Start with Your Senses: Always perform a thorough visual, auditory, and olfactory inspection before plugging anything in. This initial assessment provides invaluable context.
- Let Data Guide, Not Dictate: Use ECM data and fault codes to create a hypothesis, not a final verdict. The codes tell you what happened, not always why.
- Validate with Mechanical Tests: Always confirm electronic data with hands-on mechanical testing. A compression test or fuel pressure reading provides the ground truth that scanners can’t see.
- Replicate the Problem: For intermittent issues, a sea trial with live data logging is non-negotiable. You have to see the failure happen in its real-world environment to solve it.
Your next step is simple. On the very next engine you work on, commit to this process. Before reaching for a single tool, spend five minutes performing a dedicated sensory inspection. Note what you see, hear, and smell.
This isn’t just about fixing engines more effectively. It’s about building a reputation for precision and becoming the trusted expert who can solve the problems no one else can. That is the foundation of diagnostic mastery.
Leave a Reply