Key Takeaways
While inboard motors offer a sleek look and powerful performance, their repair costs can be a major concern. Understanding why they cost more to service is the first step to managing your boat’s budget effectively. Here are the essential insights you need to know before you own or buy.
- Accessibility is the primary cost driver, not the price of parts. You’re often paying more for the mechanic’s time to reach the engine than for the actual repair, as inboards are nestled deep inside the boat’s hull.
- Routine maintenance is consistently more expensive for inboards. Simple tasks like winterization or impeller replacement are significantly more labor-intensive and complex compared to an easily accessible outboard motor.
- Integrated systems create a “ripple effect” of risk. A simple cooling system leak can lead to catastrophic water damage to the hull and electrical systems, a danger that doesn’t exist with self-contained outboards.
- Hidden logistical costs add up quickly before the work even begins. Many inboard repairs require expensive haul-out fees and specialized mechanics who command higher hourly rates for their expertise.
- A professional installation is your best long-term investment for controlling future costs. Proper setup ensures easier service access and prevents premature wear from poor engine alignment, saving you money for years to come.
- Proactive maintenance is your best defense against expensive surprises. A consistent schedule of visual inspections helps you catch small issues early, turning a potential thousand-dollar failure into a minor, inexpensive fix.
Dive into our full guide to master these strategies and keep your inboard running smoothly without breaking the bank.
Introduction
Ever stared at a repair bill for your inboard motor and thought, “How did that simple fix cost so much?” You’re not alone. The feeling is a rite of passage for many inboard owners.
While the sleek lines and powerful performance of an inboard are undeniable, they come with a reputation for higher maintenance bills. The surprising truth? It often has little to do with the price of the parts themselves.
The real driver behind most high repair costs is something far less obvious: accessibility.
This guide gives you the expert insights needed to understand and manage your boat’s expenses. We’re pulling back the engine hatch to show you:
- Why a mechanic’s time is the biggest variable in any estimate
- A head-to-head cost comparison for common inboard vs. outboard repairs
- The hidden costs that contribute to a higher total cost of ownership
- Proactive strategies to keep your engine reliable and your budget intact
Understanding what truly drives these expenses is the first step toward controlling them. Let’s get to the heart of the matter and unpack what really makes an inboard motor tick—and what it costs to maintain.
The Heart of the Matter: Why Accessibility Drives Inboard Repair Costs
The single biggest factor influencing inboard motor repair costs isn’t the price of parts—it’s the time and effort required to get to the engine itself.
Unlike an outboard motor hanging conveniently off the transom, an inboard is nestled deep within the boat’s hull. With inboards, you’re often paying for access, not just the repair.
Unpacking the Accessibility Challenge
Engineers design boats for space on deck, not for spacious engine rooms. This creates immediate challenges for any mechanic working below deck.
Picture this: a mechanic needs to reach a simple sensor. On an outboard, it might be in plain sight. On an inboard, they could be contorting themselves into a hot, cramped engine bay just to get a wrench on it.
This difficulty leads to several key issues:
- Tight Quarters: Most inboard engine compartments are cramped, poorly lit, and difficult to maneuver in, slowing down every single task.
- Required Disassembly: A simple repair often requires removing seats, deck panels, or storage lockers first. This preliminary work significantly adds to the total labor time.
How Access Translates to Higher Labor Bills
Marine mechanics bill by the hour, and accessibility is the biggest variable in any estimate. A job that takes one hour on an outboard can easily become a three or four-hour project on an inboard due to access alone.
This isn’t just about time; it’s about specialized needs.
Working in tight spaces requires specific tools like inspection cameras and long-reach wrenches, which adds to a shop’s overhead. Furthermore, working inside the hull increases the risk of dropping a tool or causing incidental damage. Experienced mechanics factor this risk directly into their labor rates.
Ultimately, the location of an inboard transforms otherwise straightforward maintenance into a more complex and time-consuming task. Understanding that you’re often paying more for the mechanic’s time than for the parts is the key to managing your boat’s budget.
A Head-to-Head Cost Analysis: Inboard vs. Outboard Repairs
While both engine types need regular upkeep, their cost profiles for maintenance and repair are worlds apart. It’s not just about parts—it’s about the time and effort each job demands.
Here’s a practical breakdown of where you’ll feel the difference in your wallet.
Routine Upkeep: The First Cost Divide
Even simple, routine tasks highlight the accessibility gap between the two systems.
- Oil Changes: An outboard oil change is a straightforward DIY job. An inboard requires an oil extraction pump and reaching into a hot, cramped engine bay.
- Winterization: Protecting an outboard for winter is simple. An inboard needs a complex drain-and-fill of the entire cooling system to prevent a cracked engine block, leading to higher annual maintenance costs.
- Impeller Service: Replacing an outboard’s water pump impeller is easy. On an inboard, the same part might be buried deep in the bilge, turning a simple fix into a frustrating puzzle.
Common Repairs: Where the Labor Bill Grows
When common parts fail, the cost difference becomes even more stark, driven almost entirely by labor.
Picture a mechanic trying to replace a starter. On an outboard, it’s exposed and easy to access. On an inboard, that same starter might be tucked under the engine, turning a one-hour part swap into a multi-hour ordeal that inflates labor costs significantly.
Inboard-specific systems also add unique expenses:
- Exhaust Manifolds & Risers: These are common failure points from corrosion on inboards and are labor-intensive to replace. Outboards don’t have this system.
- Drive System Tuning: Inboard shafts and couplings require precise alignment. Fixing issues often means hauling the boat out of the water—an extra cost before the repair even starts.
The Worst-Case Scenario: Full Engine Replacement
This is where the financial difference is most dramatic.
A failed outboard can be unbolted from the transom and swapped with a new one in just a few hours.
Replacing an inboard is a massive surgical procedure. It often involves a crane lifting the old engine block out through the cabin floor. This process is significantly more complex and expensive, cementing the inboard’s reputation for higher-stakes repairs.
Ultimately, while inboard parts aren’t always more expensive, the difficult access and integrated systems mean you consistently pay more for a mechanic’s time. This reality shapes the total cost of ownership over the life of your boat.
The Hidden Costs of Inboard Motor Ownership
The sticker price of a repair bill is only part of the story.
Inboard ownership comes with several “hidden” or indirect costs that are crucial for a potential owner to understand. These factors contribute to a higher total cost of ownership over the boat’s lifetime.
The Ripple Effect of Integrated Systems
An inboard motor isn’t a standalone unit. It’s deeply woven into the boat’s very structure and systems, meaning one small problem can have a massive domino effect.
A simple leaking hose isn’t just an engine problem anymore—it’s a boat problem.
- Cooling System Failures: A cracked hose or failed seal in the raw water cooling system can do more than just overheat your engine. It can flood the bilge, causing catastrophic water damage to the hull, internal supports, and electrical wiring.
- Drivetrain Vulnerability: The propeller shaft passes directly through the hull. If its seal fails, it creates another direct path for water to enter the boat, posing a serious sinking risk that outboards don’t have.
- Exhaust Dangers: Leaks in the complex exhaust plumbing can release deadly, odorless carbon monoxide gas into the cabin and bilge, creating a major safety hazard for everyone aboard.
Logistics and Specialized Expertise
Beyond the engine itself, the logistics required for an inboard repair often add significant expense before a single tool is picked up.
This is where your maintenance budget can quickly get stretched thin.
- Mandatory Haul-Out Fees: Many critical repairs, especially anything involving the drivetrain or through-hull fittings, simply can’t be done in the water. Getting your boat pulled by a marina can cost several hundred dollars before the repair work even begins.
- Finding a Specialist: Complex inboard systems demand a mechanic with specific training and diagnostic tools. These technicians are often harder to find and command higher hourly rates for their specialized knowledge.
When owning an inboard, you’re not just managing an engine; you’re managing an entire integrated marine system. Factoring in these indirect costs for haul-outs, specialized labor, and potential collateral damage is essential for understanding the true financial commitment.
Smart Strategies for Managing Inboard Motor Costs
While inboards can be more complex to service, you’re not helpless against high repair bills. Proactive ownership is the key.
This approach shifts the dynamic from reacting to expensive problems to managing predictable, routine upkeep.
The Foundation: Expert Installation
The best way to manage future costs is to start right. A professional installation is the single greatest investment you can make in your engine’s long-term health.
Cutting corners at this stage almost guarantees years of costly problems.
A quality installation focuses on a few key areas:
- Planning for Access: A good technician thinks about future service, ensuring key maintenance points like filters, pumps, and belts are as accessible as possible.
- Perfect Engine Alignment: Precise alignment with the propeller shaft is non-negotiable. Even slight misalignment causes vibrations that destroy transmissions, bearings, and engine mounts over time.
- Proper Ventilation: Engine bays need powerful ventilation to manage heat and fumes, which can degrade belts, hoses, and wiring.
Your Best Defense: Proactive Maintenance
Think of routine maintenance as your best defense. A consistent schedule is crucial for catching small issues early, before they have a chance to become major, expensive failures.
Picture this: You open the engine hatch for a five-minute check before heading out. You spot a small coolant drip from a loose clamp. Tightening it costs nothing, but ignoring it could lead to an overheated engine and a thousand-dollar repair bill.
Your proactive checklist should include:
- Regular Visual Inspections: Before every outing, look for belt dust, fluid drips, loose clamps, or corrosion.
- Focus on “Weak Links”: Pay special attention to parts known to wear out, like the raw water impeller (replace annually) and exhaust manifolds (inspect every few years).
- Annual Professional Service: Have a certified mechanic perform a thorough annual inspection to spot developing issues you might miss.
Know Your Limits: DIY vs. Calling a Pro
Knowing when to grab your tools and when to call a mechanic is a critical skill for an inboard owner.
Some tasks are perfect for a hands-on owner:
- Changing the oil (with an extraction pump)
- Checking belt tension
- Cleaning out the raw water sea strainer
However, for critical systems, hiring a professional is a smart financial decision. Always call a pro for jobs involving engine alignment, through-hull fittings, fuel system integrity, or complex electrical diagnostics where a mistake could lead to a fire or sinking.
Ultimately, controlling inboard motor costs isn’t about avoiding repairs entirely—it’s about your approach. Investing in a proper installation and committing to a preventative maintenance schedule gives you the power to keep your boat reliable and your expenses predictable.
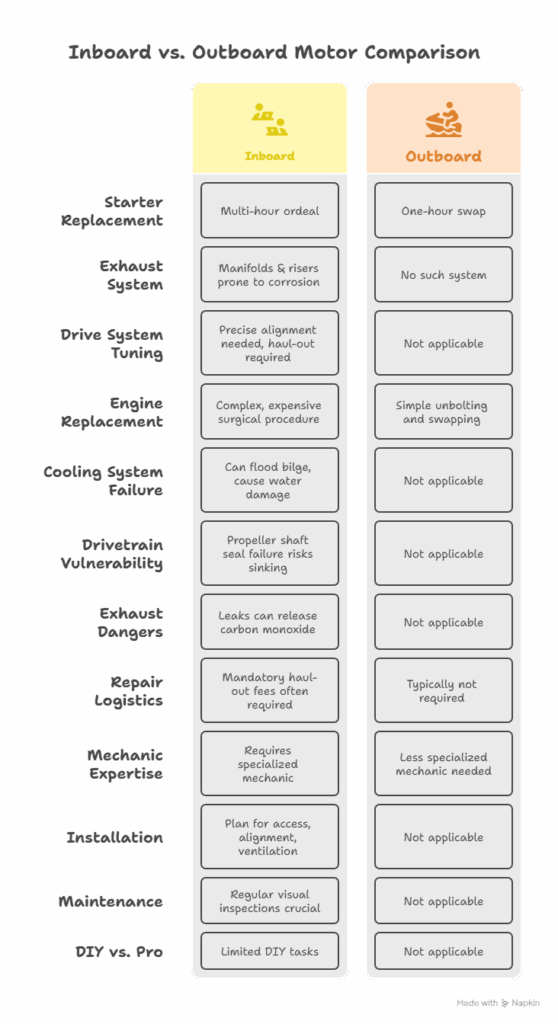
Conclusion
The reality of inboard motor ownership isn’t about accepting higher repair bills—it’s about taking control of them. While the challenges of accessibility are real, they don’t have to dictate your budget or your peace of mind on the water.
By shifting your mindset from reactive repairs to proactive management, you can transform a potential liability into a reliable, well-understood asset.
Your Key Takeaways
- Accessibility Is the Main Cost Driver: Remember that you are often paying for the mechanic’s time to get to the engine, not just for the parts themselves.
- Prevention Is Cheaper Than Reaction: A consistent maintenance schedule is your best defense against the small issues that grow into expensive, trip-ending failures.
- Factor in the Hidden Costs: Your total cost of ownership includes haul-out fees, specialized labor, and the risks associated with integrated systems like cooling and exhaust.
- Know Your DIY Limits: Tackle simple tasks to save money, but always call a certified pro for critical jobs involving engine alignment, fuel systems, or through-hull fittings.
Your Next Steps
Your journey to smarter ownership starts now. Before your next trip, take five minutes to open the engine hatch and perform a visual inspection for any drips, loose belts, or signs of corrosion.
Next, find a reputable, certified marine mechanic in your area—before you need one. Having a trusted expert on call is one of the smartest investments you can make.
Ultimately, mastering your inboard motor isn’t a chore; it’s the foundation of a confident, stress-free relationship with your boat. Take charge of your maintenance, and you’ll spend more time enjoying the water and less time worrying about what’s happening below deck.
Leave a Reply